Do you have corrosion damage or need a material suggestion? Please contact us.
We will be happy to work for you in the following areas:
- Investigation of the corrosion mechanism
- Analysis of the corrosion product or corrosion medium (e.g. drinking water analysis)
- Material research and material recommendations
- Advice on corrosion protection
- Dezincification test on brass samples according to DIN EN ISO 6509-1
- Stress corrosion cracking test according to DIN EN ISO 7539
Application example: Testing the Testing the dezincification resistance of brass of brass
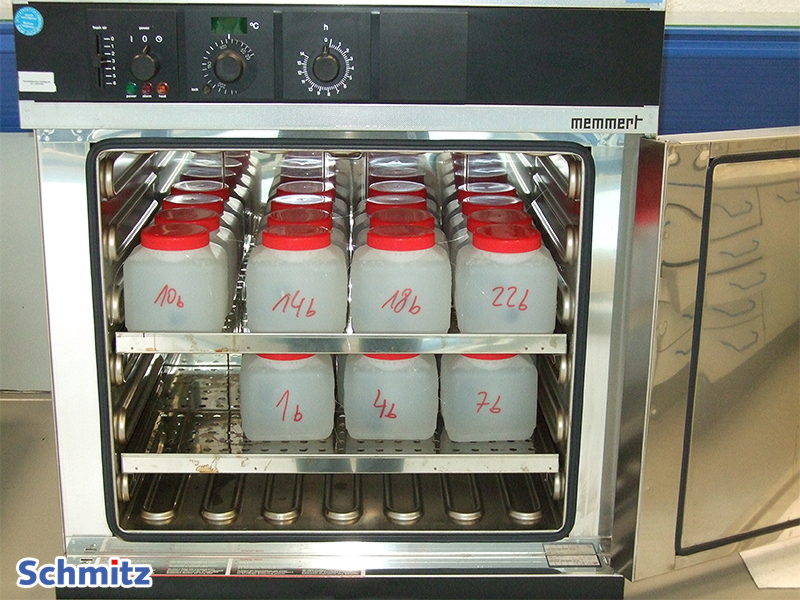
In our laboratory, we carry out tests on the dezincification resistance of brass samples (according to DIN EN ISO 6509-1). You can see what dezincification can cause in a component in the next application example.
Application example: Failure of a water pipe fitting due to dezincification
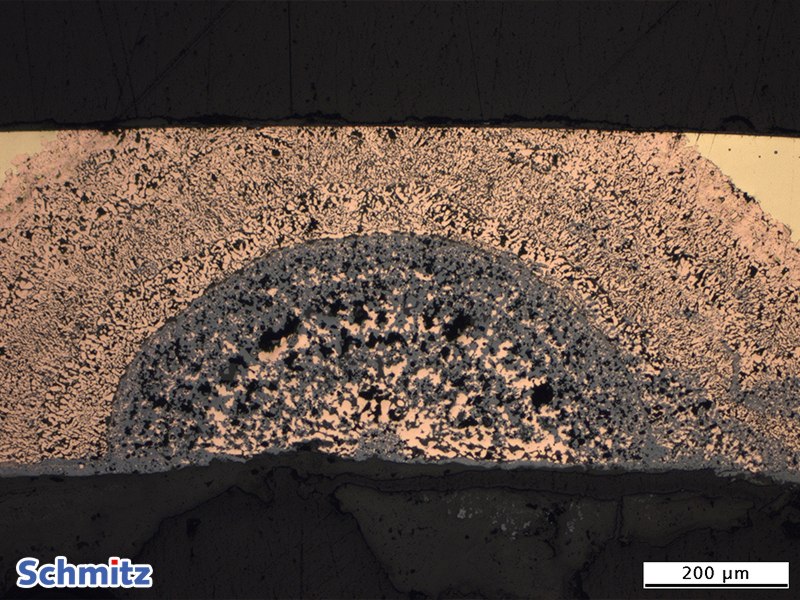
This brass tube crumbled almost completely due to dezincification. When dezincified, the brass dissolves (yellow), the zinc corrodes (blue-gray), and the copper is segregated as pure but now spongy metal (reddish).
Application example: Stress corrosion cracking (SCC)
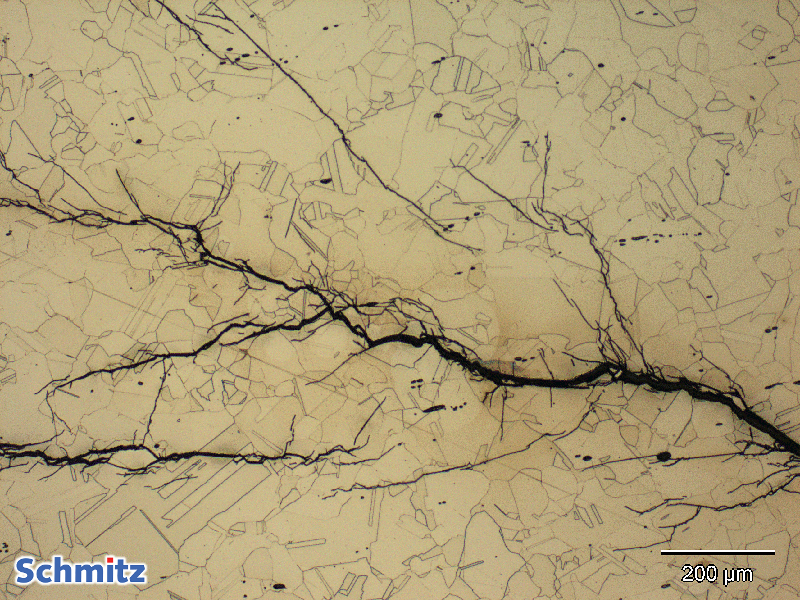
The welded rotor flange made of a high-alloy CrNi steel failed after only a short period of operation. Through metallographic microsection and EDX analysis, we were able to identify chlorine-induced stress corrosion cracking as the corrosion mechanism. A typical feature of SCC is the strong, transcrystalline branching of the cracks.
Application example: Spongiosis
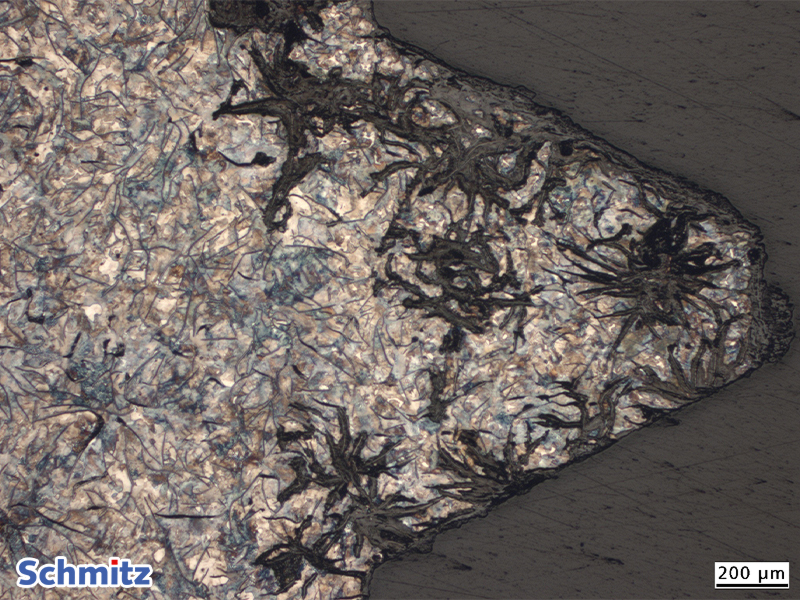
Spongiosis is a form of selective corrosion of cast iron in which the corrosion attack progresses along the graphite-matrix interfaces and dissolves the iron matrix. In the case of long graphite lamellae, deep penetration of the corrosion is thus possible. The graphite remains and holds the corrosion product together. The original shape of the cast component is retained, but the black “iron sponge” (mainly FeOOH) no longer has any strength.
Application example: Intergranular corrosion
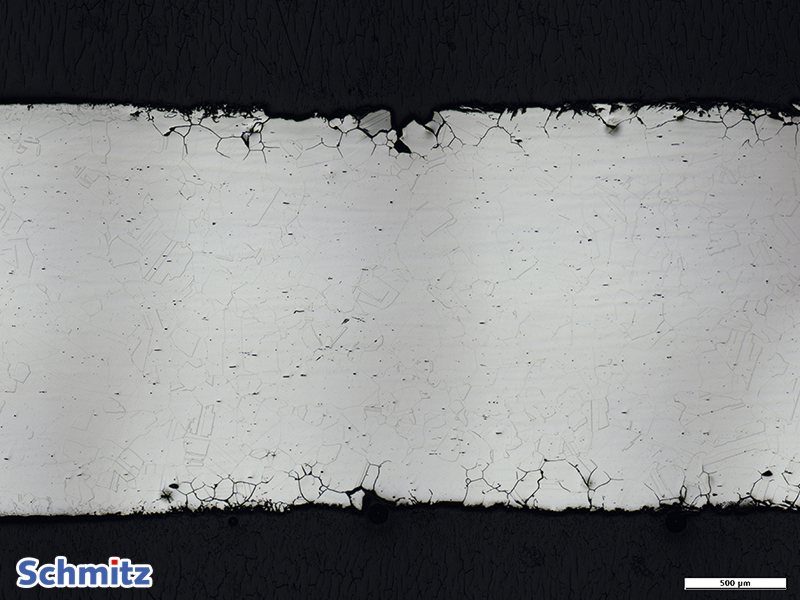
In the heat-affected zone of a welded stainless steel pipe, fine chromium carbides were segregated on the grain boundaries due to temperature. The resulting chromium depletion in the area led to local intergranular corrosion during pickling of the surface, which already noticeably weakened the wall thickness.