We supply high quality monocrystalline and polycrystalline industrial diamond powder, each batch passed our quality control.
Available grit sizes
Common grain sizes of monocrystalline diamonds range from 0.25 to 100 µm. Polycrystalline diamond powder is available from stock in grain sizes from 0.25 to 50 µm.
Other grain sizes are of course available at short notice on request.
Jump to the desired topic:
Useful background about diamonds
The term diamond comes from the Greek word “adamas”, meaning “indomitable”. This name possibly comes from the fact that diamond is the hardest natural substance in the world. In 1955, it was possible to produce artificial diamonds for the first time. Industrial diamond is as hard as natural diamond. A distinction is made between monocrystalline and polycrystalline diamonds.
Diamond powder types
Monocrystalline diamond powder
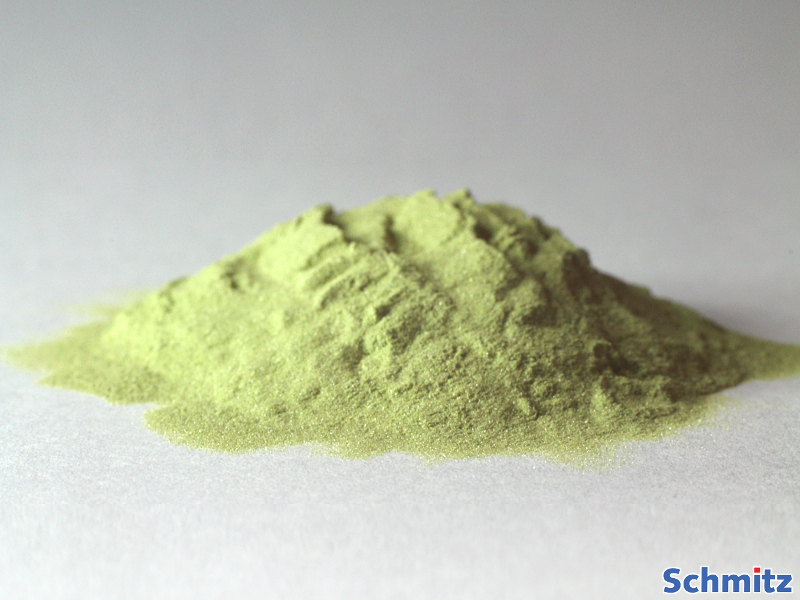
Monocrystalline industrial diamond (single crystal) is relatively inexpensive and can be produced in large quantities. Therefore, it is widely used in industrial technology in grinding, lapping and polishing processes. The diamond has a monocrystalline lattice structure, and the slip planes are oriented parallel to the optical axis (111-plane). Under load, the monocrystalline diamond grain breaks along the parallel cleavage planes. This produces grains in blocky form with sharp cutting edges. Figuratively speaking, a monocrystalline diamond grain breaks like a salami that is cut into slices (“salami slice model”).
Polycrystalline diamond powder
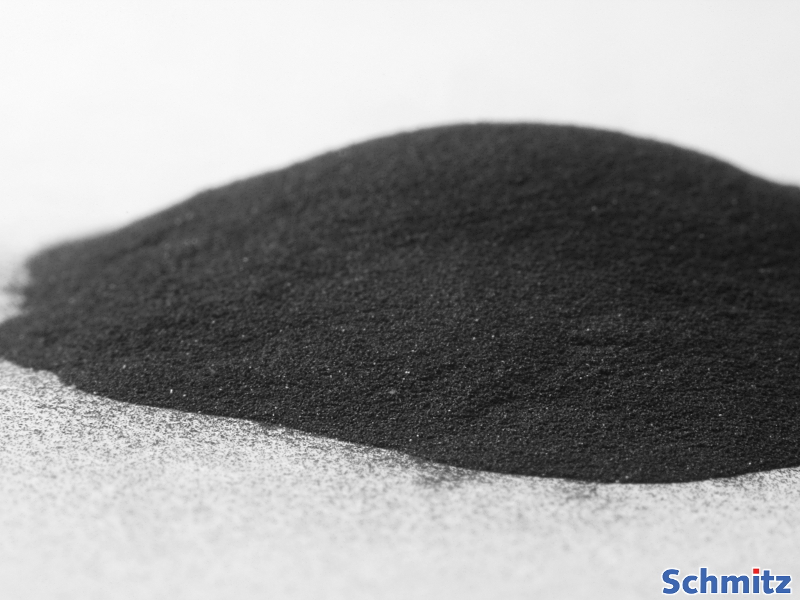
A polycrystalline (industrial) diamond (multicrystal) is composed of a large number of tiny diamond grains. Under load, small corners and edges break out of the diamond grain, so that new, sharp cutting edges are created again and again (self-sharpening effect). Thanks to this unique characteristic, maximum stock removal rates and at the same time the finest surfaces are achieved. It is suitable for lapping and polishing extremely hard materials such as ceramics or sapphire glass.
Nanodiamond powder
Nanodiamond powder is used in various applications and research fields. The large volume-to-surface ratio creates new physical and chemical properties. For example, nanodiamonds have perfect lubricating properties and are therefore added to lubricating oils. According to ISO/TS27687:2008, nanomaterials are divided into three categories:
- Nanoplate (1-D)
- Nanofibre (2-D)
- Nanoparticle (3-D)
According to ISO/TS27687:2008, only when the particle size is < 100 nm is it a nano-object. The smallest grain fraction we can supply is 0-0.1 µm (0.05 µm).
Natural diamond powder
For the sake of completeness, natural diamond powder should also be mentioned. The monocrystalline natural diamond powder is preferably used for the production of electroplated diamond tools. As a waste product of the jewelry industry, it is very rare and correspondingly highly priced. The properties of our polycrystalline paste exceed the service life and stock removal performance of other manufacturers’ pastes made from natural diamond powder.
Coated diamond powder
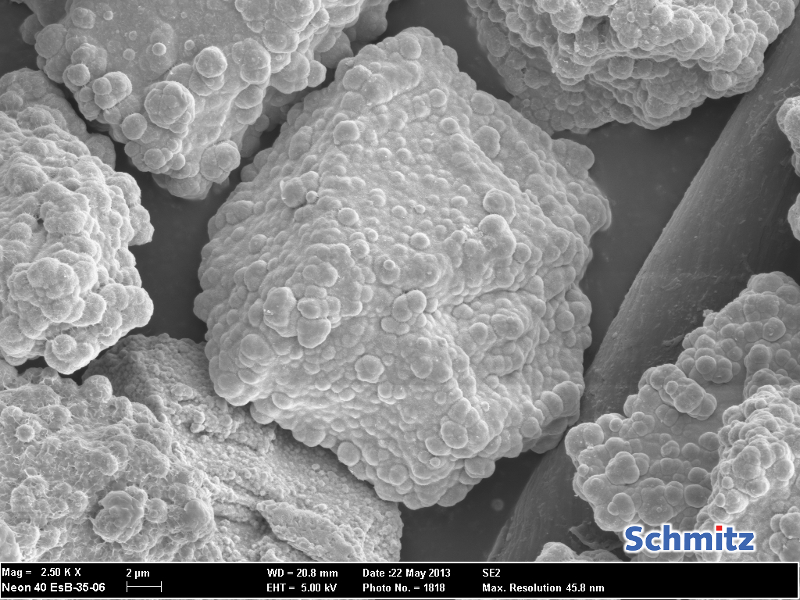
Monocrystalline industrial diamond powder coated with Ni, Cu or Ti is used (among other things) for the production of electroplated diamond tools.
Manufacturing process
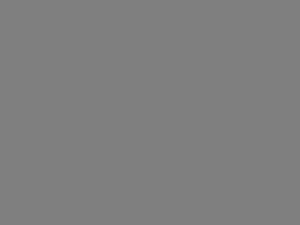
In the 1950s, for the first time, the natural conditions (high temperature and high pressure) for the formation of diamonds were successfully reproduced by a phase transformation of graphite into diamond. Artificial diamonds were produced for the first time (E. Lundblad, 1953). Since then, it has been possible to produce synthetic diamonds by a high-pressure, high-temperature process on an industrial scale. In this process, graphite is pressed in a hydraulic press (1955, General Electric) at pressures up to 6 GPa (60000 bar) and temperatures above 1500 °C in the presence of catalysts (iron, nickel, metal alloys and carbides).

The figure below shows the belt press schematically. The conversion process takes several weeks. Other processes for generating high temperatures and pressures are so-called detonation synthesis and shock wave synthesis. In detonation synthesis, a distinction is made between detonation of a mixture of graphite and explosives or detonation of explosives alone. In the latter, an explosive mixture of TNT (trinitrotoluene) and RDX (hexogen) is detonated in a sealed container. The explosive provides the required energy and is also a carbon carrier. In shock wave synthesis, the pressure required to convert carbon material into diamond is brought about by the action of an external shock wave, also triggered by an explosion. The explosion compresses a capsule filled with carbon material. This force causes the carbon material inside to be transformed into diamond.
Further processing
The synthetically produced rough diamonds are first mechanically comminuted (grinding in ball mills). Impurities from residues of the reactants on the surface of the diamond particles, such as non-combustible impurities or unconverted graphite residues, are removed chemically. Classification is done by sieving for coarser grains. Micron grains, on the other hand, must be sedimented. For this purpose, the diamond powder is placed in a water basin. Stokes’ law can be used to calculate the sedimentation rate of a spherical particle. The upper layers of the water-diamond powder mixture are carefully sucked off after a respective sedimentation period and physically dried.
Properties
The typical properties of diamond are its extreme hardness, very high thermal conductivity, high electrical resistivity and a low friction coefficient of 0.03.
Properties | Diamond natural/synthetic |
---|---|
Crystal system | cubic |
Martens hardness | > 70.000 N/mm² |
Mohs hardness | 10 |
Thermal conductivity λ | 2.300 W(mK)⁻¹ |
Electrical resistance ρ | 1014 Ωm |
Dynamic friction coefficient µG | 0,03 |
Density | 3,52 g/cm³ |
Refraction index n | ⁓ 2,43 |
Compressive modulus K | 442 GPa |
Melting point | 3550 °C |
Chemical resistance | nearly inert |
Bruch | conchoidal, splintered |