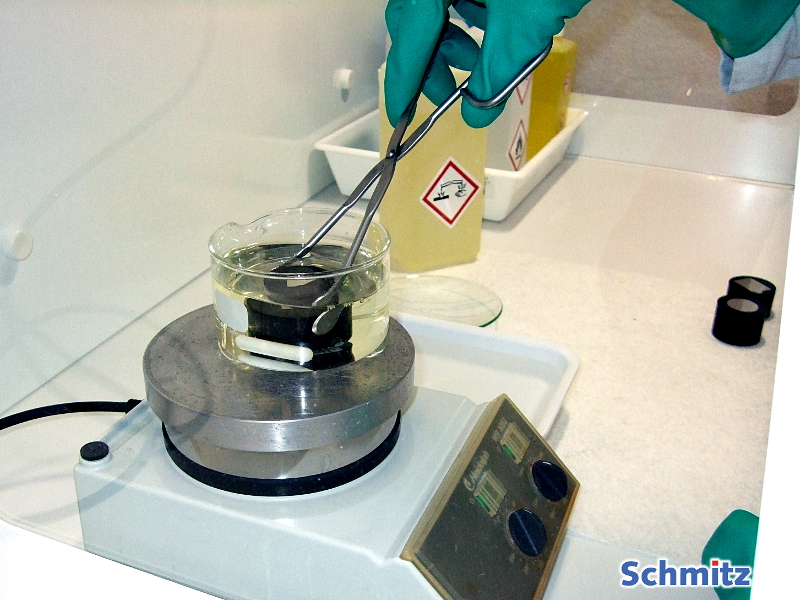
We offer a comprehensive range of etchants for metallographic microstructure contrasting. We can currently offer you 20 different etchants as well as suitable accessories. The scope of the assortment is adapted according to demand. Our etchants are always freshly prepared. We supply special echants as a kit, so that you can mix them yourself shortly before etching.
Is your etchant not included? If you require special formulations (e.g. according to SAE Aerospace Material Specification, GE Aviation), we will be happy to produce them for you. However, for smaller purchase quantities, the costs for a safety data sheet, the PCN message (emergency number) and the UFI code must be included in the calculation.
The safety data sheets for the individual etchants can be found here.
Jump to the desired topic:
Macroetching
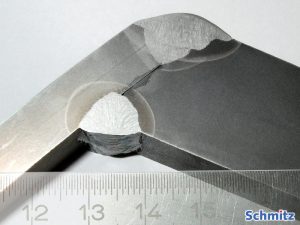
Etchings imaged up to approx. 30 times magnification are referred to as macroetchings. This requires a macrosection with a finely ground (wet grinding) or slightly polished surface. Macroetching is used to make visible the primary cast structure, forging and rolling textures as well as segregations or the contour of welded joints. In addition to general macro etching, other process variants of macroetching include deep etching and the impression method (Baumann print).
Macroetching agents
TIP // You are not sure which etchant is the right one for your material? Take a look at our microstructure database. There you may find the right material and can see which agent we have used to etch it.
Your material is not listed? Contact us and we will help you select the right etchant.
Adler
The Adler macroetching agent is suitable for cast iron, high-alloy and corrosion-resistant steels as well as nickel alloys for visualization of welded joints and coarse grit. A finely ground surface (wet grinding) to at least P600 grit is required. For visualization of fine details (remelting cracks in Cr/Ni steel), it is recommended to grind to P1200 and briefly polish to 3 µm PanTec.
Heyn
Heyn is a macro etchant rarely used nowadays to detect phosphorus segregations in steel. The phosphorus segregations are etched brown by the copper ammonium chloride solution. The copper precipitate that forms is removed under running water by rubbing with absorbent cotton. Repeated etching and wiping enhance the contrast.
Spot test with Heyn
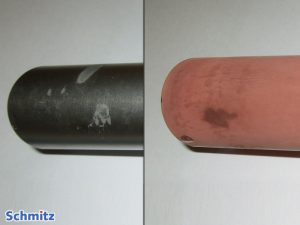
The presence of a dense compound layer on (gas)nitrided workpieces can be determined by means of the spot test. The surface of the test piece must be free of grease. Cleaning in several steps is recommended. The test specimen is completely immersed in a copper ammonium chloride solution (Heyn etchant). The immersion time is about 0.5-2 minutes. If the compound layer is thick enough (about 10-15 µm), the original blue color of the reagent is retained for at least 2 minutes. In the case of thin (5 µm) or porous layers or if no compound layer is present, a color change to red becomes visible after a short exposure time. Partial component discolorations indicate an uneven layer thickness. The cause may be, for example, insufficient pre-cleaning before the nitriding process (drying spots) or component contact (e.g. nitriding as bulk material). The red coloration is due to a chemical reaction. Copper is forced out of its compound – (NH4)2[CuCl4]-2H2O – by iron. This causes the free copper on the steel surface to precipitate. The spot test is a non-destructive testing method. Polished surfaces, however, become dull.
TIP // The duration of the test and the indication is strongly dependent on the surface of the component as well as the volume of the etchant. In order to be able to make a reliable statement about the presence of the compound layer, a series of tests with at least 50 specimens would have to be examined.
If you want to assess the quality of your nitrided layer, we can alternatively offer you a metallographic section including analysis of the compound layer and the porous zone (according to DIN 30902 or AWT/FA5-AK3). Simply contact us for this.
Nital
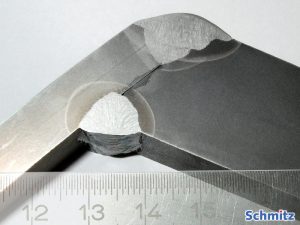
Nital is a macro etchant for weld joints and heat affected zone for mild and low alloy steels.
You can obtain the following variants from us:
TIP // Do you have problems with rapid overetching of your welds? You can also use a 3% nital solution for macro etching.
Oberhoffer
Oberhoffer is macro etchant for detecting phosphorus segregation (fiber flow) and visualizing the dendritic microstructure in steel. The effect of the etchant is based on the fact that a thin, firmly adhering copper skin forms on the phosphorus-rich areas, which prevents acid attack. The P-segregations are not etched (thus remain white). Copper precipitation the low-phosphorus ferrite is just prevented, so that these areas are etched. By repeated intermediate polishing and renewed etching, the contrast is significantly increased.
Microetching
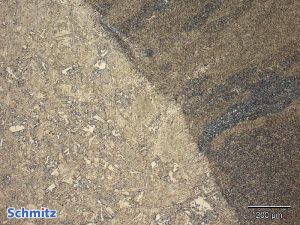
For visualization of the (secondary) microstructure by means of microscopic imaging procedures from approx. 50x magnification. Two main methods are distinguished: wet chemical and electrolytic (more on electrolytic etching: see below). In addition, a differentiation is made between grain boundary and grain surface etching. Microetching can be performed using various techniques.
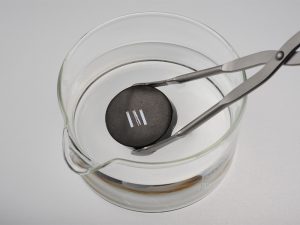
The most widely used method of wet chemical etching is the so-called dip etching.
In this process, the microsection is completely immersed in the etching solution. The microsection should be agitated in the etching solution with the etching tongs in order to destroy the resulting hydrogen bubbles and to compensate for any differences in the concentration of the etchant.
Some dip etchings require heating of the etchant (e.g. V2A-etching solution).
In ambulatory metallography, wipe etching or wash over is used. In this process, the specimen is rubbed with a cotton swab dipped in the etchant or carefully drizzled with it.
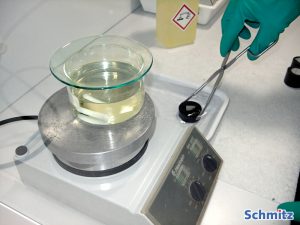
TIP // Avoidance of etching spots:
Gaps or cracks often have to be infiltrated in order to prevent etch spots due to the etchant being absorbed and concentrated in these cavities. In this case, we recommend wetting the ground surface with the respective base of the etchant (water or alcohol) before etching. In this way, the gap is infiltrated and the etchant cannot accumulate there. A post-infiltration with wax has proven to be impractical for us, as it is not suitable for use in hot V2A etching, for example, due to its low melting point.
Microetching agents
TIP // You are not sure which etchant is the right one for your material? Take a look at our microstructure database. There you may find the right material and can see which agent we have used to etch it.
Your material is not listed? Contact us and we will help you select the right etchant.
Brass etchant
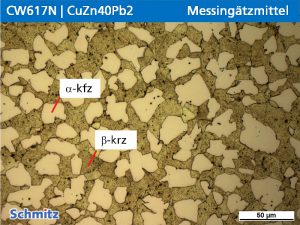
This water-based etching reagent for brass is excellent for CuZn alloys, CuBe Alloys or pure copper. It is equally suitable for pure alpha brass as well as alpha-beta brass. The beta phase is colored.
Klemm’s I and Klemm’s II
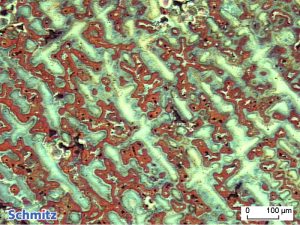
Klemm’s-I is a color etchant for non-alloy and low-alloy steels and cast irons. Klemm‘s-II, on the other hand, is suitable for copper alloys and soft solder joints (see picture on the right). Both etches can only be viewed under polarized light.
The etching solution must always be freshly prepared for both variants (can only be kept for a few hours). You will receive a kit consisting of a stock solution (saturated sodium thiosulfate solution) and potassium disulfite. Klemm-I and Klemm-II are constructed identically, only the amount of potassium disulfite to be added varies:
- Klemm-I: 100 ml stock solution + 2 g potassium disulfite
- Klemm-II: 100 ml stock solution + 5 g potassium disulfite
Kroll’s
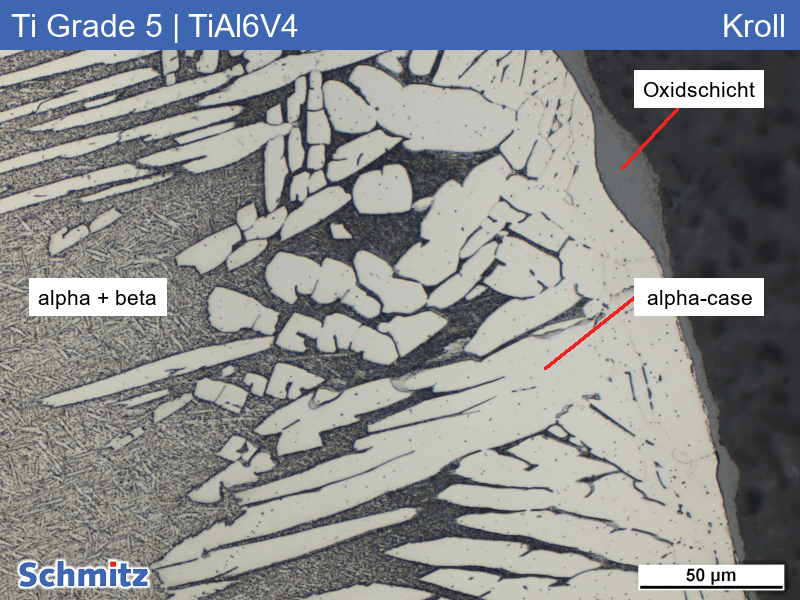
Kroll’s is a microetching agent for Al-Cu alloys and titanium alloys (e.g. Ti6AlV4).
CAUTION // Kroll etchant contains hydrofluoric acid. Therefore, please observe the regulations for handling hydrofluoric acid when using it! For your safety, we offer an anti-hydrofluoric acid solution which is suitable as first aid in case of burns with hydrofluoric acid and should be part of the basic equipment in every metallographic laboratory.
Kroll, modified according to RolceRoyce specification RPS 150
This etchant corresponds to the formulation in Appendix 2, Etchant 2a. The concentration varies slightly from the standard concentration and therefore also has a different GHS classification than our normal Kroll. It is suitable for etching titanium and its alloys. A separate safety data sheet with UFI number is available and can be downloaded here.
CAUTION // Kroll etchant contains hydrofluoric acid. Therefore, please observe the regulations for handling hydrofluoric acid when using it! For your safety, we offer an anti-hydrofluoric acid solution which is suitable as first aid in case of burns with hydrofluoric acid and should be part of the basic equipment in every metallographic laboratory.
Nital
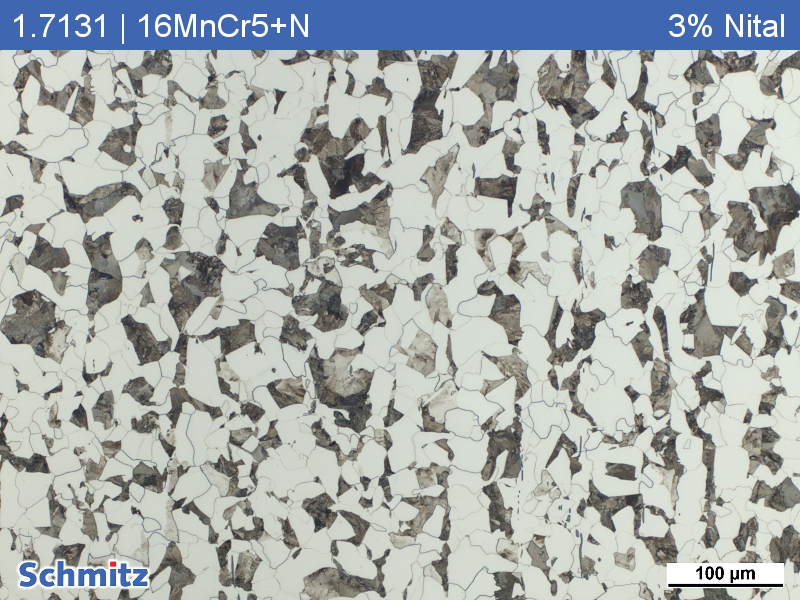
Nital is the standard microetching agent for microstructure development of ferrite, pearlite, sorbite, troostite and martensite on unalloyed and low-alloyed steels and cast irons.
It is available in the following variants:
V2A etching solution
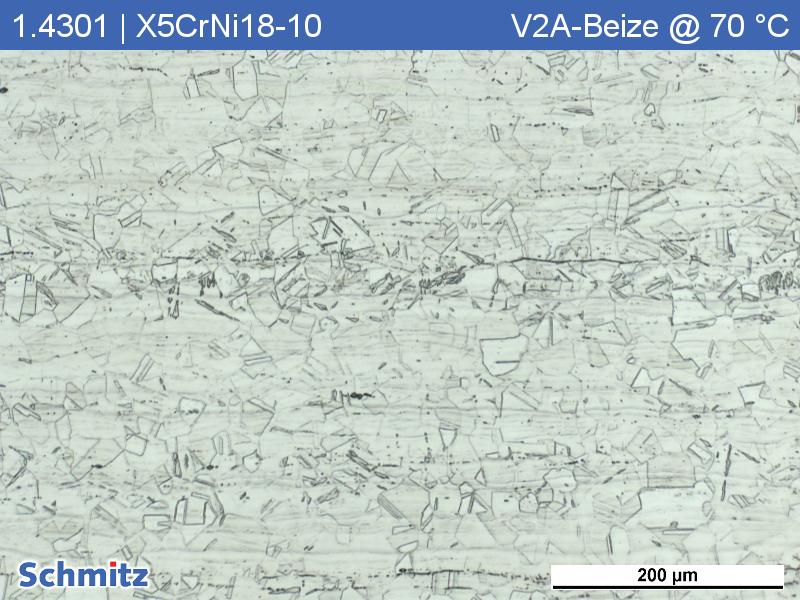
V2A etching solution is a standard microetching agent for high-alloy chromium-nickel steels and similar welding consumables as well as austenitic cast materials. It is often heated to approx. 70 °C to ensure more effective and faster attack of the etching solution.
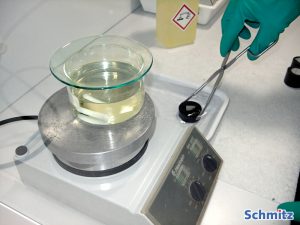
TIP // Avoidance of etching spots:
When using heated etchants, there are often problems with unwanted etch spots on the ground surface. This occurs mainly at cross-section transitions, as the dissimilar cross-sections heat up at different rates. Warmer spots are etched faster than colder spots, resulting in a gradient.
You can avoid this as far as possible by preheating the ground specimen in hot water before dipping it into the warm etching solution. This ensures that the surface of the ground sample has approximately the same temperature as the heated etchant. This gives you a more uniform etch attack.
When heating etchant, you should place a watch glass on the etch tray to prevent evaporation.
Electrolytic etching
In electrolytic etching (also known as anodic etching), a direct current is applied between the sample, which here acts as the anode, and a cathode (e.g., a V2A sheet). Both electrodes are in an electrolyte, in this case an etchant.
Positively charged metal ions leave from the ground surface due to the applied voltage and pass into the electrolyte; an equivalent number of electrons remain in the sample and are discharged. Thus, direct material removal of the material occurs. If the metal ions leaving the sample surface react with ions from the etchant and form insoluble compounds, in addition to the material removal, a top layer with different thicknesses (depending on the orientation and composition of the microstructural constituents) can also be formed. Thus, the individual grains/phases of the material are contrasted.
TIP // You want to prepare and etch specimens on an outpatient basis? Our ambulant grinding and polishing device (MobiPol) is also available with an optional etching pencil.
Etchants for electrolytic etching
Barker
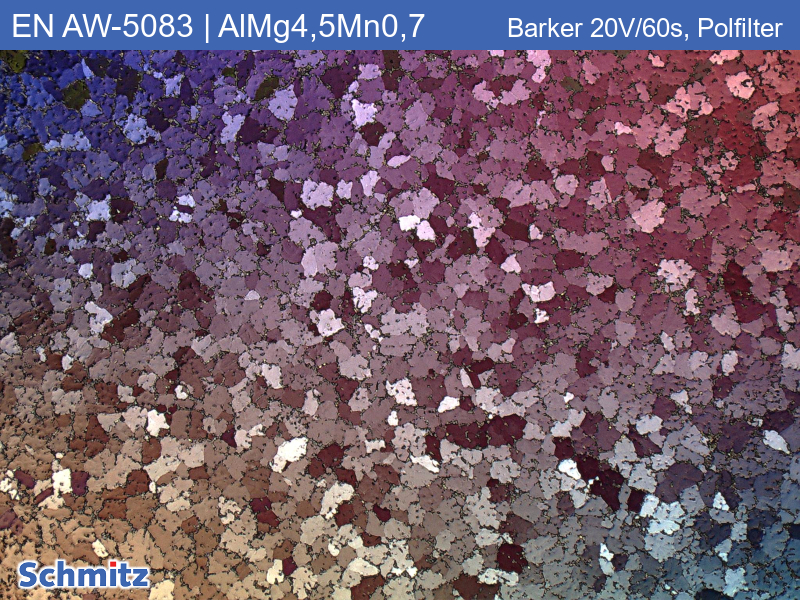
Barker is an electrolytic etchant for pure aluminum and aluminum alloys (5000 series alloys). Barkered aluminum specimens must be viewed in polarized light.
Parameters: 1-2 minutes at 20-40 volts. For example, we etch an EN AW-6005A alloy for 2 minutes at 24 volts.
For reference images of barbed specimens, you can take a look at our microstructure database.
TIP // A complete set for etching with Barker (including a DC voltage source, etching vessel and etchant) can be found here.
INSTRUCTIONS// The etching vessel (V2A cathode/cup) is connected to the negative pole, the ground joint surface/specimen (banana plug/pin) is connected to the positive pole. The positive pole can also be connected to the etching pliers using an alligator clip.
NaOH 5%
NaOH 5% can be used for steels as electrolytic detection of the sigma phase. The sigma phase is initially colored yellowish to dark brown, followed by the coloration of the ferrite. After a certain etching time, the carbides in the microstructure are also developed.
Parameters: 5-60 seconds at 1-3 volts.
Oxalic acid
Oxalic acid can be used as an electrolytic etchant for Cr and CrNi steels. The microstructure is developed. The sigma phase is dissolved away, while carbides are only slightly attacked.
Parameters: 5-20 seconds at 1.5-3 volts.
Internal processes during etching
The etching of a metallic microsection is a chemical or electrochemical process. Due to local differences in the chemical composition, local currents are formed as a result of potential difference. The individual phases/grains are dissipated to different extents or contrasted by a fine precipitation skin. An etching attack due to crystal orientation also takes place. Due to the different dissipation rates of the individual microstructural constituents, a relief is created. The incident light undergoes a reflection change at the phase boundaries.
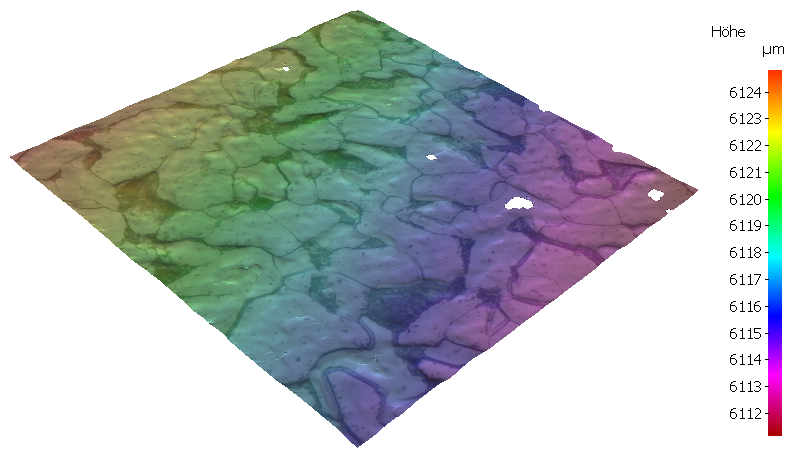
The height difference of the crystal faces is up to 500 nm, which then form the “cast shadow” of the grain boundary. On the right, a measurement result from the white light interferometer.
Accessories
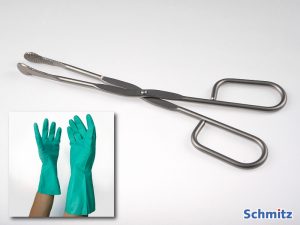
We have the right accessories for etching on offer for you. These include:
- Anti hydrofluoric acid solution
- Etching bowls
- Etching tongs
- Beakers
- Safety gloves
- Ethanol
- Face shields
- Isopropanol
- Laboratory protective aprons
- Timer
- Safety glasses
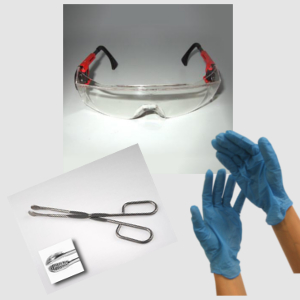
Particularly practical: our initial equipment including face shield or safety glasses, etching tongs and chemical protection gloves.
- Original equipment for macro etching (with face shield)
- Original equipment for micro etching (with safety glasses)