Is your component too large and cannot be brought to our laboratory?
No problem, we can also come to you.
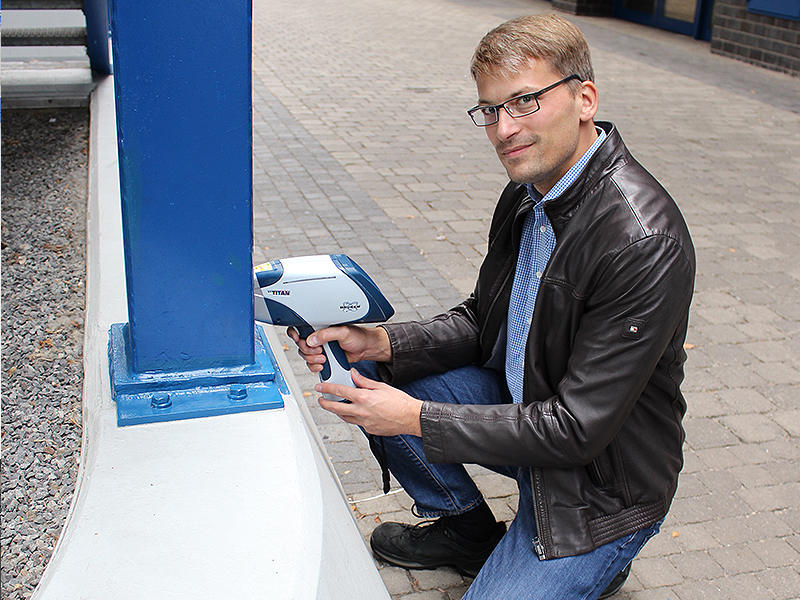
With our mobile handheld XRF spectrometer, we can non-destructively analyze the chemical composition of your component or, for example, your buildup weld. In the Aachen area, we are the first to be able to offer you this service.
It is also possible for us to perform a microstructure examination on your component by means of ambulatory metallography or a mobile hardness measurement.
In our laboratory, in addition to XRF analysis, we can also perform radio spectral analysis (OES) to determine the chemical composition of your samples.
Contact us for an individual offer.
Analytical methods:
X-ray fluorescence spectroscopy (XRF)
X-ray fluorescence analysis (XRF) is one of the most widely used methods for the qualitative and quantitative determination of the elemental composition of a wide variety of materials, as it is non-destructive and requires no special sample preparation.
Possible materials
The method is suitable, among other things, for the analysis of
- Metals and alloys
- Soil samples, rocks, slag
- Magnetic materials
- Jewelry, coins, art objects or precious metal ingots
- Electronic components and soldering
- Metallic abrasion in gear oils
Functional principle

The sample is excited by X-rays, knocking electrons out of shells close to the nucleus (1). The gap is immediately filled by an electron from a higher orbital (2). The energy difference is released in the form of an X-ray quantum (3), which is collected by a detector.
Each element has a set of characteristic X-rays. By evaluating the spectrum, one can infer the concentrations of the elements. The lightest element detectable by XRF is magnesium (atomic number 12). The detection limit is about 1 ppm.
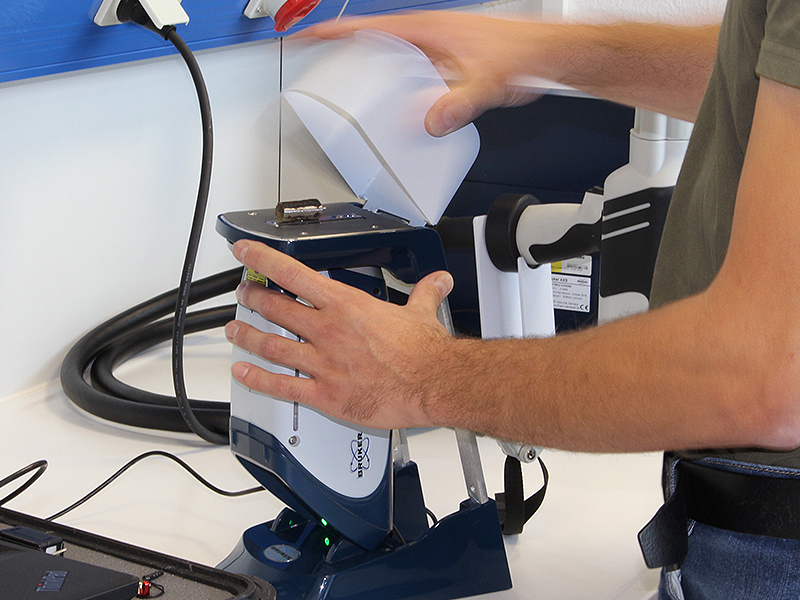
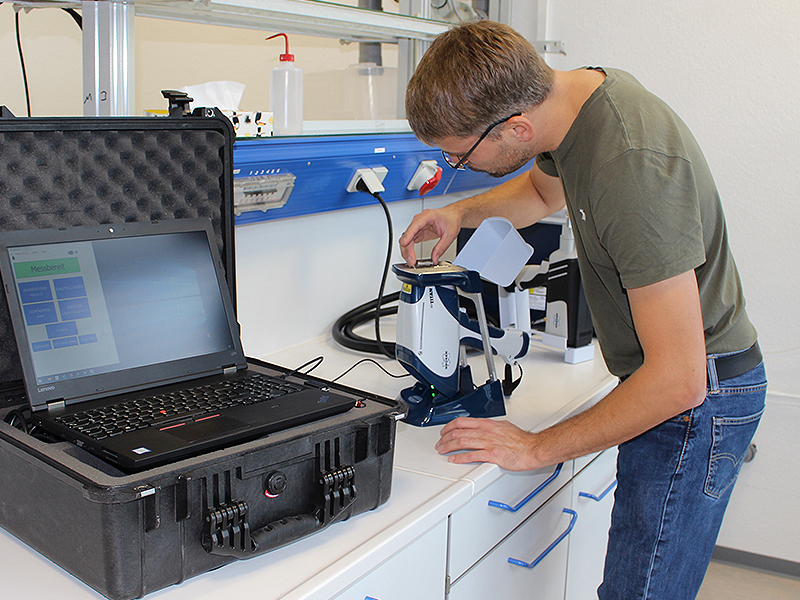
Optical emission spectroscopy (OES)
Optical emission spectrometry (spark spectral analysis) is one of the oldest physical methods for determining the chemical composition of metals.
Which metal alloys can we analyze?
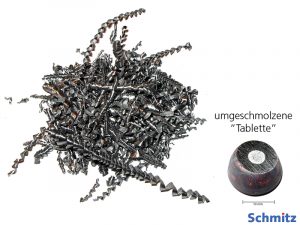
- Iron-based alloys (and cast iron after prior sample remelting for white solidification)
- Aluminum alloys
- Copper alloys such as brass or bronze
- Nickel-based alloys
- Titanium alloys
A flat analysis surface of ideally several cm2 is required. The minimum surface area is 6 mm in diameter. Smaller samples such as powder or chips must be remelted inductively.
Functional principle
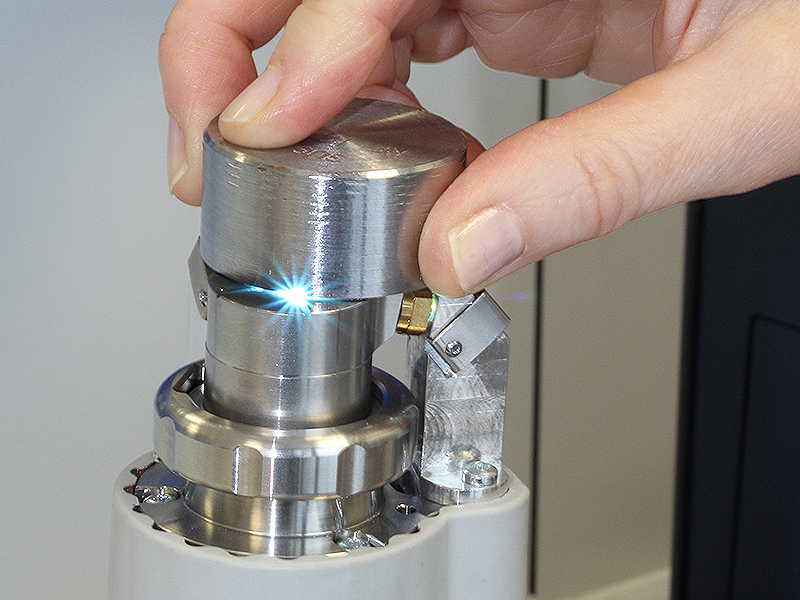
Each electron is characterized by a specific energy level. If energy is supplied to an atom, e.g. in the form of heat by means of an electric arc, the electrons are transferred to an unstable “excited” state (a higher energy level), from which they quickly fall back to the ground state. In the process, the previously absorbed energy is released again in the form of light of a characteristic wavelength.
An electric arc is ignited between the tungsten electrode and the test specimen under an argon veil and the specimen surface is vaporized. The emitted radiation is split into the individual wavelengths in the optics of the spectrometer; detectors measure the light intensities, from which the element concentrations are calculated.
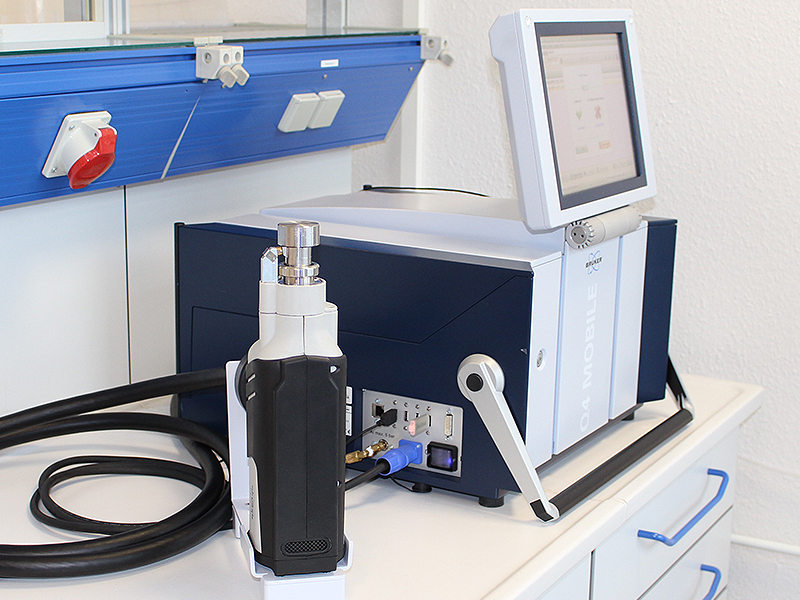
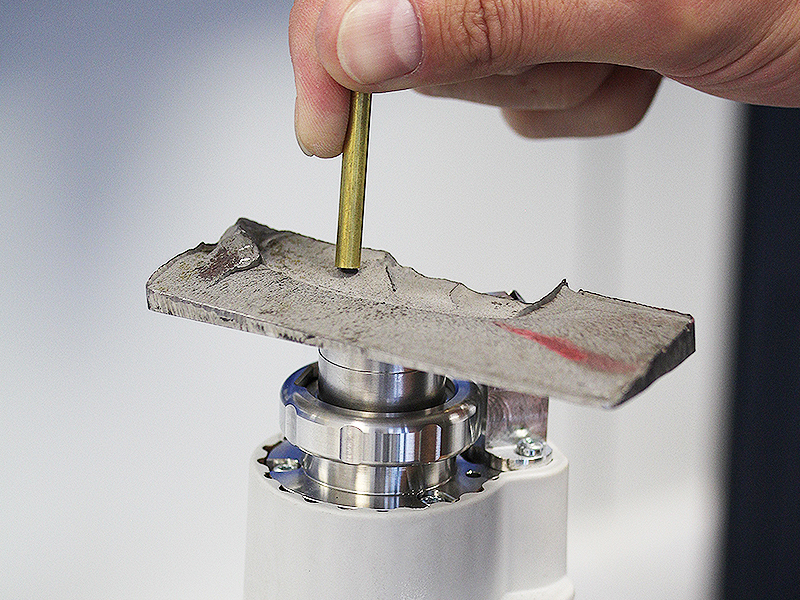