Hält Ihr Bauteil, was es verspricht?
Die klassische Werkstoffprüfung ist auf dem Gebiet der Schadensfalluntersuchung unerlässlich.
Wir stellen Ihnen gerne ein individuelles Angebot mit den verschiedensten Untersuchungsmethoden zusammen. Kontaktieren Sie uns dafür einfach.
Folgende Untersuchungen gehören zu unserem Standard:
Zerstörende Werkstoffprüfung
- Härteprüfung nach Brinell, Vickers, Rockwell und Shore D
- Ermittlung der Einsatzhärtungstiefe (CHD) und Nitrierhärtetiefe (NHD)
- Zugversuch gemäß DIN EN ISO 6892-1
- Kerbschlagbiegeversuch nach DIN EN ISO 148-1 (- 196 °C bis + 200 °C)
Zerstörungsfreie Werkstoffprüfung
Insbesondere bei der zerstörungsfreien Werkstoffprüfung bieten wir nur ausgewählte Methoden im Rahmen von Schadenuntersuchungen an. Ultraschall-, Magnetpulver- oder Wirbelstromprüfungen gehören nicht zu unserem Repertoire.
Verfahrensbeschreibungen
Brinell gemäß DIN EN ISO 6506-1
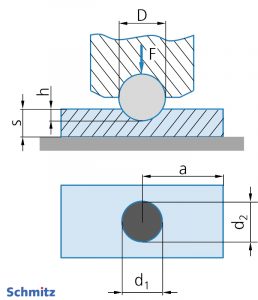
Bei der Härteprüfung nach Brinell wird ein kugelförmiger Eindringkörper aus Hartmetall dem Beanspruchungsgrad entsprechend langsam und stoßfrei in den Prüfkörper gedrückt. Der entstandene kalottenförmige Prüfeindruck wird nach Wegnahme der Prüfkraft vermessen. Der Quotient aus Prüfkraft zur Eindrucksoberfläche ist das Maß für die Härte. Vorteil des Verfahrens sind die repräsentativ großen Prüfeindrücke zur Härteermittlung heterogener Werkstoffe, wie z.B. Gusseisen.
[Bildquelle: Füllmann, R.: Der Werkstoffprüfer, ISBN 978-3-00-054275-6]
Vickers gemäß DIN EN ISO 6507-1
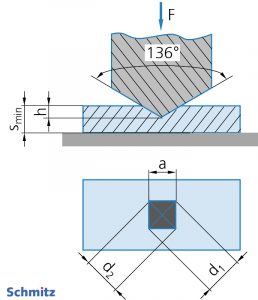
Bei der Härteprüfung nach Vickers wird ein pyramidenförmiger Eindringkörper mit quadratischer Grundfläche aus Diamant langsam und stoßfrei in den Prüfkörper gedrückt. Der entstandene rautenförmige Prüfeindruck wird nach Wegnahme der Prüfkraft vermessen. Der Quotient aus Prüfkraft zur Eindrucksoberfläche ist das Maß für die Härte. Vorteil des Verfahrens ist die Prüfung über den gesamten Härtebereich von „weich bis extrem hart“.
[Bildquelle: Füllmann, R.: Der Werkstoffprüfer, ISBN 978-3-00-054275-6]
Einsatzhärtungstiefe (CHD) gemäß DIN EN ISO 18203
Die Einsatzhärtungstiefe (ehemals Eht) nach dem Aufkohlen und Härten ist der senkrechte Abstand (in mm) von der Oberfläche bis zu der Tiefe, die eine Grenzhärte von 550 HV aufweist.
Anwendungsbeispiel: CHD-Bestimmung an Sinterzahnrad
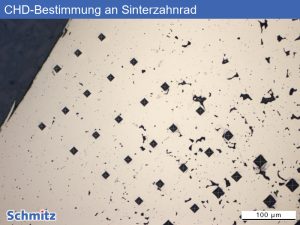
In pulvermetallurgisch gefertigten, porösen Werkstoffen führen wir den Härteverlauf fünfreihig durch. Härteeindrücke, die zu dicht an Poren sitzen, werden bei der Nachkontrolle aussortiert, so dass auch hier die Einsatzhärtungstiefe vernünftig ermittelt werden kann.
Nitrierhärtetiefe (NHD) gemäß DIN EN ISO 18203
Die Nitrierhärtetiefe (früher Nht) ist der senkrechte Abstand (in mm) von der Oberfläche eines nitrierten Bauteils bis zu dem Punkt, wo die Vickershärte einem festgelegten Grenzwert entspricht. Die Grenzhärte liegt bei Kernhärte (KH) + 50 HV (nach oben gerundet auf 10 HV).
TIPP// Untersuchung von Nitrierschichten: Wir bieten Ihnen gerne auch eine metallographische Untersuchung der Nitrierschicht inklusive Bestimmung des Porenanteils und Messung der Dicke der Verbindungsschicht an (gemäß DIN 30902 bzw. AWT/FA5-AK3). Kontaktieren Sie uns dafür einfach.
Randschichthärtungstiefe (SHD) gemäß DIN EN ISO 18203
Die Randschichthärtungstiefe ist der senkrechte Abstand (in mm) von der Oberfläche eines randschichtgehärteten Bauteils bis zu dem Punkt, wo die Vickershärte einem festgelegten Grenzwert entspricht. Die Grenzhärte (GH) berechnet sich zu: A × erforderliche minimale Oberflächenhärte (HV). A ist dabei ein Faktor, für den üblicherweis 0,8 eingesetzt wird. In einem Abstand von dreimal der SHD sollte die Härte mehr als 100 HV unterhalb der Grenzhärte liegen.
Rockwell gemäß DIN EN ISO 6508-1
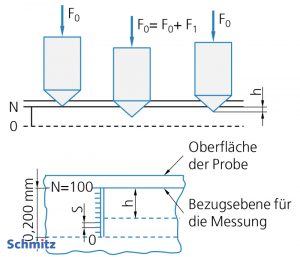
Bei der Härteprüfung nach Rockwell wird ein kegelförmiger Eindringkörper aus Diamant oder ein kugelförmiger Eindringkörper aus Hartmetall langsam und stoßfrei in das Werkstück gedrückt. Nach Entlastung der Prüfzusatzkraft wird die Eindringtiefe direkt auf einer Messuhr angezeigt. Vorteil des Prüfverfahrens ist die schnelle und einfache Durchführbarkeit.
[Bildquelle: Füllmann, R.: Der Werkstoffprüfer, ISBN 978-3-00-054275-6]
Shore D gemäß DIN ISO 7619-1
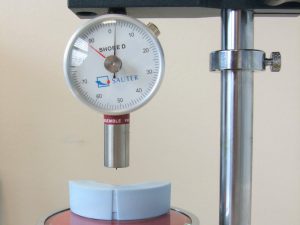
Die Shore-Härte dient zur Härtecharakterisierung von Kunststoffen. Die bekanntesten Varianten sind Shore A (für weiche Kunststoffe wie z.B. Gummi) und Shore D (für harte Elastomere). Die Skala der Härtewerte reicht jeweils von 0 bis 100. Bei der Härteprüfung nach Shore D dient eine Stahlnadel mit einer kugelförmigen Spitze (Radius 0,1 mm) und einem Öffnungswinkel von 30° als Eindringkörper. Diese wird mit einer Anpresskraft von 50 ± 0,5 N in die Probe gedrückt; als Maß für die Härte dient die Eindringtiefe nach 15 s. Ein Härtewert von 0 entspricht der maximalen Eindringtiefe von 2,5 mm, der Härtewert 100 einer Eindringtiefe von Null. Die Dicke des Prüfkörpers sollte mindestens 6 mm betragen. Das Durometer kann auch mobil eingesetzt werden.
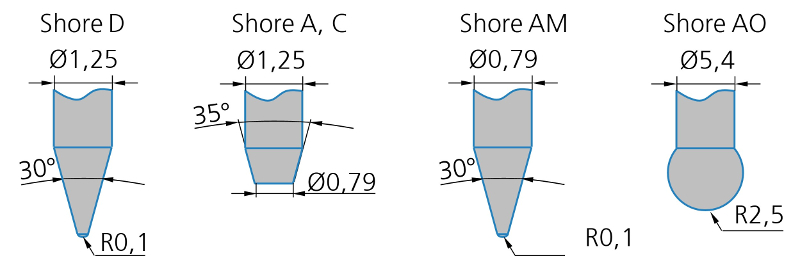
[Bildquelle: Füllmann, R.: Der Werkstoffprüfer, ISBN 978-3-00-054275-6]
Zugversuch gemäß EN ISO 6892-1
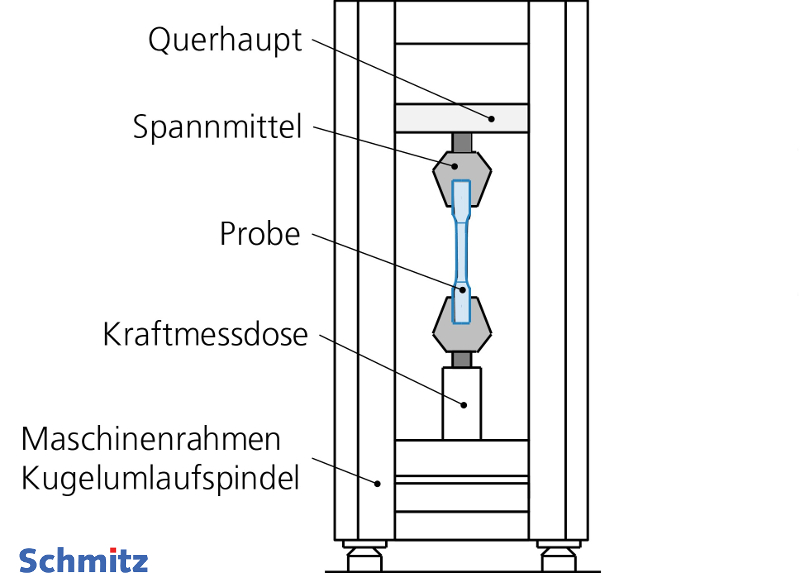
Der Zugversuch ist eines der wichtigsten Versuche in der Werkstoffprüfung. Er dient der Ermittlung von mechanischen Kennwerten bei einachsiger, gleichmäßig über den Querschnitt verteilter Zugbeanspruchung. Dazu wird eine Probe mit genormter Geometrie langsam, gleichmäßig und stoßfrei gestreckt, bis der Bruch eintritt. Dabei wird kontinuierlich die Kraft und Verlängerung der Probe erfasst. Aus Quotient von Kraft und Ausgangsquerschnittsfläche wird die Spannung, aus der Längenänderung die Dehnung der Probe errechnet.
[Bildquelle: Füllmann, R.: Der Werkstoffprüfer, ISBN 978-3-00-054275-6]
Kerbschlagbiegeversuch gemäß EN ISO 148-1
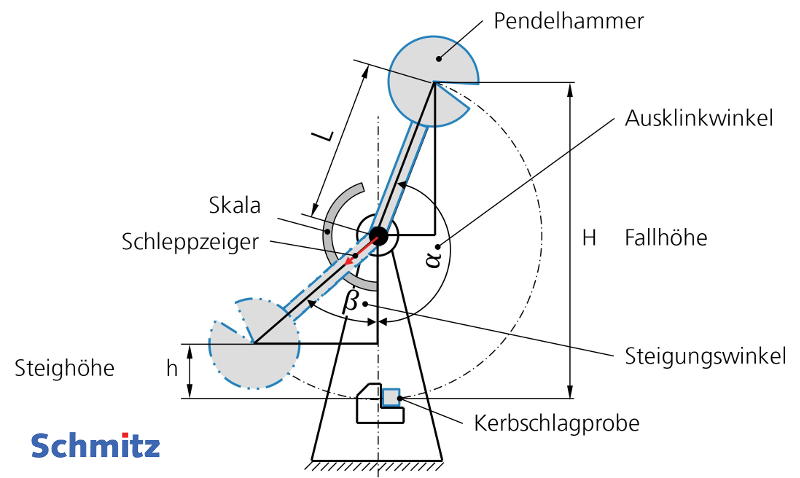
Der Kerbschlagbiegeversuch dient der Ermittlung der Zähigkeit eines Werkstoffs bei schlagartiger Beanspruchung. Hierzu wird eine mittig gekerbte quadratische Probe mit einem Pendelschlagwerk zerschlagen. Die dabei verbrauchte Schlagenergie ist das Maß für die Zähigkeit des Werkstoffs.
[Bildquelle: Füllmann, R.: Der Werkstoffprüfer, ISBN 978-3-00-054275-6]
Eindringprüfung gemäß DIN EN ISO 3452-1
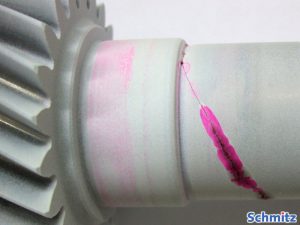
Hierbei handelt es sich um ein zerstörungsfreies Oberflächenprüfverfahren auf Risse und Poren. Wir nutzen dieses Verfahren z.B. zur Festlegung von Trennschnitten, um Anrisse zu öffnen. Die kontrastreiche Eindringfarbe dringt durch Kapillarwirkung in die Oberflächendefekte der gereinigten Probe ein. Nach erneutem Säubern wird ein Kontrastmittel aufgetragen, welches die Eindringfarbe aus den feinen Hohlräumen heraussaugt und Fehlstellen so sichtbar macht.
Schleifbrandprüfung (nach AMS2649, Typ I und II)
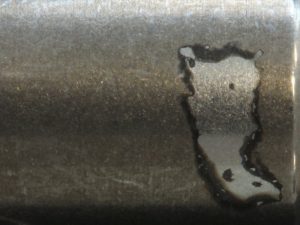
Die Schleifbrandprüfung dient dazu, lokal überhitzte Zonen auf martensitischen Stahloberflächen zu entdecken. Eine Überhitzung entsteht beispielsweise bei schleifender Bearbeitung oder Schweißen der Proben und kann zu einer Neuhärtung und/oder Erweichung der beanspruchten Bereiche führen. Bei der Schleifbrandprüfung werden die gereinigten Proben in HNO3 geätzt, es folgen Sichtprüfung und Dokumentation.
Da die Prüfung einen sehr geringen Materialabtrag von weniger als 1,5 µm verursacht, wird sie den zerstörungsfreien Verfahren zugeordnet. So können nicht nur Stichproben, sondern gesamte Chargen geprüft werden.